Amcor Expanding Thermoforming Capacity for Medical Packaging
The company’s Oshkosh, Wisc., facility is making a sizable investment in new thermoforming equipment to answer demand in North America.
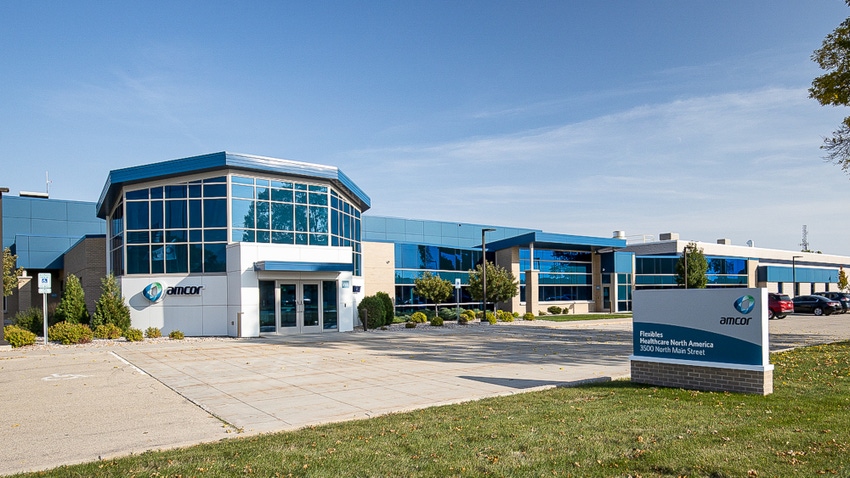
Amcor will be adding thermoforming equipment to its Oshkosh, Wisc., plant. The new equipment will be installed in the facility’s Class 7 cleanroom and is expected to be operational as early as December 2024. The cleanroom operates under the ISO 13485 quality system.
This move will support increasing demand from customers in the medical, pharmaceutical, and consumer health sectors for thermoforms and lids.
Art Castro, Vice President and General Manager for Amcor Flexibles North America (AFNA) Healthcare, gives us more details about the expansion.
What specific equipment will be installed in the Oshkosh plant?
Castro: We’re adding multiple best-in-class, automated thermoforming machines designed to meet the stringent requirements of healthcare applications. The plant’s expanded cleanroom also will be able to support additional thermoforming lines in the future.
What is the cost of the capital investment?
Castro: This is a significant investment.
What will be the plant’s production capacity after the expansion, and what percentage increase is that from today?
Castro: Oshkosh Healthcare is one of the world’s largest manufacturing plants for sterile barrier medical packaging materials. This investment adds thermoforming as a new production capability for the site.
Why is there growing demand for healthcare packaging in North America?
Castro: The medical technology industry is rapidly developing less-invasive surgical procedures that involve innovative new tools. These tools have packaging requirements that can benefit from the protection of a custom design tray and lid.
In the pharmaceutical industry, there’s a growing need to protect new, high-value medications with quality trays.
The press release says, “The expansion also will allow customers to source thermoforms and companion die-cut lids from a single location, helping streamline product manufacturing and distribution.” Why is this a benefit? Don’t most medical companies have a primary and secondary source for critical components, which includes deliberately sourcing them from separate manufacturing locations?
Castro: Most custom thermoforms used in sterile medical device applications require a companion custom-designed lid for product protection and ease of removal within surgical settings. Sourcing these items as a one-to-one system — meaning, in the same order and shipment — provides a simplified supply chain solution for our customers.
About the Author(s)
You May Also Like