New Packaging Code to Revolutionize Parenteral Pharmaceuticals
The SignaKey code, smaller than Data Matrix, allows you to track sterile injectable drugs — at the unit level — from container manufacturing through the supply chain. But that’s not all it does.
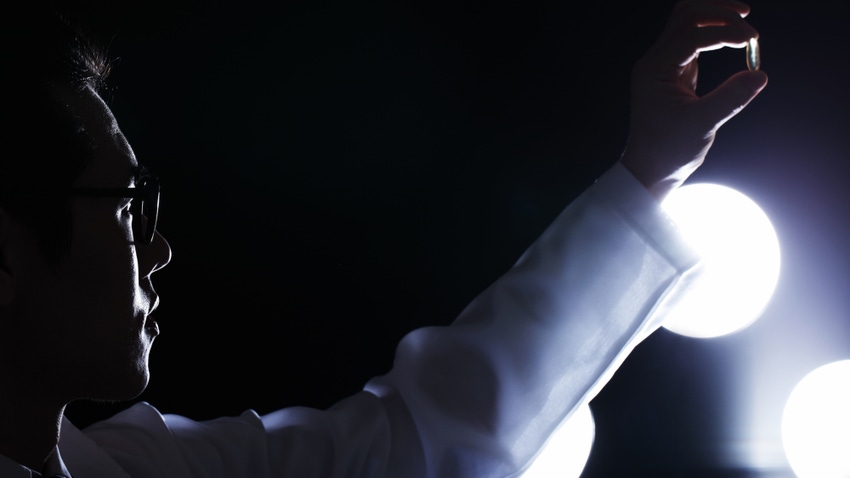
At a Glance
- SignaKey could enable zero false rejects during visual inspection, a major improvement in aseptic manufacturing efficiency
- Produced with an ultra-high-frequency laser, SignaKey is embedded into container walls without impacting material properties
- SignaKey works with range of glass or plastic pharmaceutical packages: vials, syringes, cartridges
“With my experience pioneering unit-dose and serialization coding applications for pharmaceuticals — and then in the last five years focusing on improving overall aseptic operations — I can share that if I was still leading a technology group supporting sterile operations, I’d be championing SignaKey as a major initiative,” says Rich Hollander.
Hollander is semi-retired and a consultant now, after a 32-year career with Pfizer, lastly as VP, Sterile Injectable Technology. He’s been hired to help share the news about SignaKey.
What is SignaKey? SignaKey is a two-dimensional coding technology that’s simple yet robust and can be used for a variety of markets. SignaKey has already been proven in several industries — including parenteral pharmaceuticals, automotive and cannabis — for more than a decade. This versatility positions SignaKey as a cutting-edge solution with potential applications beyond the pharmaceutical sector. But it particularly fits the unique needs of sterile pharmaceuticals.
Like other coding technologies, track-and-trace and anti-counterfeiting are advantages of SignaKey. But Hollander gets most excited about its operational benefits.
An example of a standout operational advantage of SignaKey’s code is the potential for getting to the aspirational goal of zero false rejects during a product’s Visual Inspection process. “If we could uniquely identify each glass component as it goes through visual inspection,” Hollander supposes, “we could potentially get to zero false rejects in that operation, [which are] major sources of loss in aseptic manufacturing and potentially unnecessary investigations.”
SignaKey’s solution permits precise data about an ejected package as captured images can now be tied to a specific container. And because you will know why a package has been ejected, you can make better decisions for accepting or rejecting it. Imagine the savings in time and money.
Produced with a femtosecond laser (an ultra-high-frequency laser widely used in ophthalmic surgeries), the SignaKey code is embedded into a container wall — without any physical impact to the material. For parenteral pharmaceutical packages, such as glass vials, this means there are no chemical or physical changes to the glass container. Product quality is maintained.
A key advantage of this ultra-high-frequency laser is its ability to mark codes inside the glass wall without any physical impact or alteration of the glass’s chemical properties.
SignaKey codes can be embedded in glass or plastic (including cyclic olefin copolymer, aka COC), making this a single coding technology that can be used for vials or syringes, or any typical package used for sterile pharmaceuticals. And it’s impervious to damage from rough handling because the code is embedded in the package and not printed on it. In addition, due to its low contrast, it will not interfere with existing automated visual inspection processes.
SignaKey also withstands the pharmaceutical depyrogenation cycle, the process of removing pyrogens such as bacterial endotoxins from sterile injectable drugs. Syringes are not subjected to depyrogenation, so this isn’t an issue for this packaging format. Data Matrix codes, however, disappear when containers are subjected to the high temperatures of depyrogenation.
By putting the code inside the container wall, SignaKey ensures a level of security and traceability that surpasses traditional methods.
What is the SignaKey code?
Highly compressed, the SignaKey code is a grid of 256 characters, plus one row and one column of orientation symbols. Each character is the letter Y, positioned in one of four ways: up, down, left, right. The permutations that can be printed are virtually endless, making it suitable for producing enough codes for unit-level serialization.
Dr. Richard McDermott, SignaKey CEO, puts it this way: “The European Space Agency estimates there are between 10 to the 22nd and 10 to the 24th stars in the entire cosmos. If you take the highest of those numbers, SignaKey can produce 5.2 billion times more marks than there are stars in the cosmos. So, I don’t think in Rich’s lifetime or my lifetime we’re going to run out of numbers.”
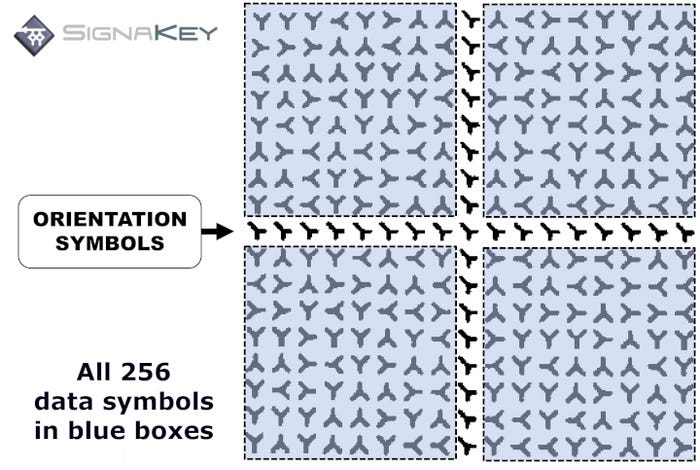
SignaKey
If you were to encode a numeric code of 12 digits, a SignaKey can be printed much smaller than a Data Matrix code — 0.8 millimeters vs 1.2mm. SignaKey could carry far more data than 12 digits at this size, but this size has been optimized for best overall marking and reading rates. And up to 60% of a SignaKey code this size could be compromised and still be readable. Additionally, SignaKey can be read by conventional lenses.
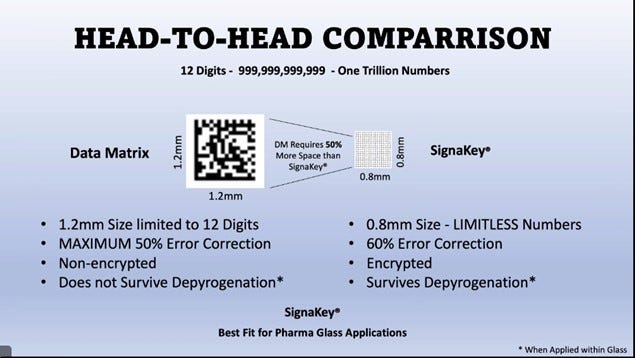
SignaKey
The code can be printed with any coding technology. But for parenteral pharmaceuticals, SignaKey has worked closely for more than a decade with LASEA, a French company supplying femtosecond laser equipment. LASEA has already used its femtosecond laser coding equipment to print Data Matrix codes for a pharmaceutical application (see video). In use, LASEA has marked SignaKey at speeds that equates to 333 codes/packages per minute.
Video shows femtosecond laser code in practice for parenteral pharmaceuticals. The code marked in this case was a Data Matrix. But the technology, proven here, is the same for the SignaKey code.
Another advantage of a SignaKey code embedded into the container wall with an ultra-high frequency laser is that the small code is printed flat, eliminating readability issues associated with codes printed on a curved surface.
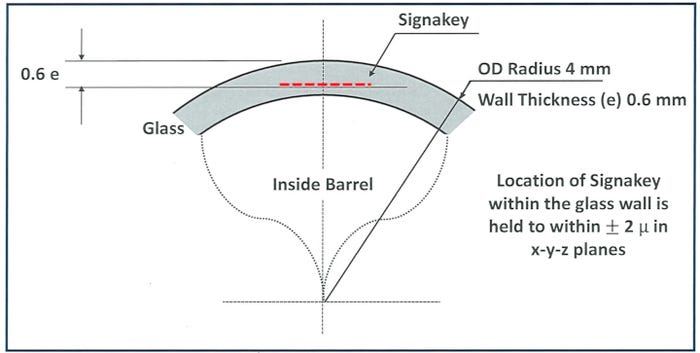
SignaKey
“Everything we’ve been doing is targeting the most challenging item that we have,” Hollander says, “which is the 1-milliliter syringe because of the wall thickness and the radius.”
Industry support for UID is strong and widespread.
SignaKey is poised to redefine industry standards by providing a solution for unique identification (UID) of primary containers used in injectable pharmaceuticals — vials, syringes, and cartridges, glass or plastic.
UID is an issue the International Society of Pharmaceutical Engineering (ISPE) has been working on. From the ISPE Discussion Paper Unique Identification on Primary Containers to Drive Product Traceability & Quality | ISPE | International Society for Pharmaceutical Engineering:
“Today, all glass containers are identical during manufacturing operations, be it component forming, product filling, visual inspection, or device assembly, making it challenging to proactively identify problematic locations with their processes when an issue is observed. The implementation of a UID (Unique Identifier) strategy for primary packaging containers would change this by allowing for single container visibility throughout the manufacturing process location, thus enabling focused root cause analyses and continual improvement activities.”
The ISPE working group is poised to issue a guidance document for “Parenteral Container Traceability” in the first half of 2024. This collaborative effort involves major pharmaceutical companies, glass converters, equipment manufacturers, medical device manufacturers, and serialization solution providers. The industry’s mobilization around this initiative indicates a recognition of the untapped value associated with container traceability.
The UID concept is also supported in the updated version of the USP <1790> Visual Inspection of Injections document.
Hollander says, “If for some reason we have a field incident reported, such as a crack or particulate, the time required to investigate would be dramatically reduced. Today, we sift through batch data at [each] manufacturing step. In the future, the batch could theoretically be that unit itself as we could have the specific quality data for not just that container from the point of creation at a supplier, through filling, inspection, and packaging, but for each container associated with that batch.”
Compare that to today’s process. If a healthcare practitioner notifies a manufacturer of a crack in the glass, that triggers an investigation to confirm whether it is an isolated event or if there might be something larger present.
Hollander explains, “While all glass containers are inspected throughout the processes of the glass converter, as well as the manufacturer, glass is glass, and it has a memory. If banged around enough, flaws that cannot be seen can cause cracks. If the crack goes through the glass, it can compromise a product’s sterility.
“Until a manufacturer completes the investigation, it may be necessary to put all product still in their control, that was filled into containers from the same batch of implicated glass, on hold. Investigations like this take significant time and effort as engineers sift through batch data from throughout the process to support making the proper decision for the affected product.
“But …,” Hollander continues, “if there’s a serial number on cracked container, we could quickly go back to the batch and container data, both at the glass supplier, as well as every other step in the manufacturing process, and review not just that container’s data, but look at data to the north and south around that container to see if there were any signals that might indicate a portion of a batch may have had an issue that was not captured via standard in-process inspection data.
“Having this type of tool will not just speed up an investigation but will provide a new level of data granularity to support decision making, and also more accurately define when an issue began and ended. When viewed together, container traceability can improve product quality and also minimizes the amount of potentially perfectly good product that we might otherwise choose to reject.”
The industry must weigh the pros and cons of different serialization carriers, such as radio frequency identification (RFID) in syringe needle shields and Data Matrix codes printed on glass vials and syringes. SignaKey advocates for an open and inclusive approach, emphasizing that the success of container traceability depends on widespread adoption.
What might your investment in SignaKey be?
The infrastructure for UID for primary containers exists and the industry has successfully completed Proof of Concept. As we move into the implementation phase, we must assess the benefits and costs.
We’ve gone through the benefits of SignaKey. What about the costs?
“Pharma companies are extremely cost sensitive and dubious of ‘softer’ value actually making it into a cost standard and showing the ROI [return on investment]. So, to enable adoption, cost has to be nominal and far outweighed by the value it creates,” Hollander says. “Adoption could be phased and targeted. For example, one could start by simply using it for bright stock product mix-up detection during packaging — a relatively simple and immediate implementation. Solution providers, the same ones that work in the end-of-line serialization space, are already aiming to help companies better leverage machine-level data that is available today. They have expressed strong interest in what this, combined with what they already offer, could do.”
SignaKey CEO McDermott advocates for the glass converter to apply the SignaKey code during package manufacturing — “on the back end of their annealing lines from their converting operations,” adds Hollander. This would provide additional quality control benefits throughout the supply chain and minimize the pharmaceutical manufacturer’s investment.
McDermott itemizes the economics this way:
• According to LASEA, the two cameras used in the video to read the Data Matrix were “dumb” devices, about $1,000 each, as opposed to “smart cameras” with features such as liquid lens, at a cost of $15k to $20k each. LASEA says dumb cameras would work equally well for reading the SignaKey code.
• If the glass converter marks vials/syringes, they will select the cameras.
• If the pharma manufacturer plans for full aggregation, multiple dumb cameras would be required at each touch point.
• For prefilled syringes (PFS), McDermott says the automated vision inspection (AVI) supplier could tie in the captured images to individual containers.
Hollander says having direct digital access to critical dimensions for every container produced by a supplier, along with images, should mitigate the need to perform dimensional inspection during incoming inspection — “provided the process for gathering, storing and sharing data is properly qualified and, as needed, validated.” That would save time and minimize labor.
If you are a pharma manufacturer and would like to see your packaging suppliers add the SignaKey code, tell them. The chances of the packaging manufacturer adding the code is much higher if they know customers are interested.
With three-decades of experience working for a major pharma manufacturer, Hollander knows, “When we serialized packages at the logistical level to help mitigate counterfeiting, implementation costs were high. The return on that investment to internal operations … well, most companies have yet to see measurable value. As we learn how we could use serialization upstream of the retail package, it becomes easy to appreciate that, compared to anti-counterfeiting investments made over the last 15 years, the capital required to read, capture, and leverage data at the container level would be far less — yet the value gained to operations, significant.”
Hollander admits, “Yes, there will be an upcharge for the containers to be marked. But over time, and with scale and market competitiveness, that cost should also become negligible.”
“Yes, there will be an upcharge for the containers to be marked. But over time, and with scale and market competitiveness, that cost should also become negligible.”
Right now, we have a little bit of a chicken or egg situation. Pharma manufacturers that would like to pilot in this space need container manufacturers to be able to provide marked containers. And before container manufacturers invest in new technologies, they would like to know there is customer interest.
SignaKey is working with glass converters to add the SignaKey code at a reasonable cost and without impacting yield, as well as with pharma manufacturers to ensure they are aware of the value in container traceability and how the SignaKey fits overall for all container types used in aseptic operations.
On the software side, McDermott tells us, “We have been in discussions with two solution providers — each a recognized industry leader in the US and Europe. Their systems already handle all the required data flow, both upstream and downstream, including aggregation. Some new computer code would be needed to reach up the supply chain to the glass converter. But neither thought that insurmountable.”
How SignaKey stacks up.
To reiterate, potential uses and benefits of SignaKey to enable container traceability include:
• To speed up investigations, improve decision making, and reduce quarantine and reject quantities;
• To identify process “drifts” and react more quickly to trends;
• To reach zero false rejects during visual inspection by having insight into why packages are ejected;
• To mitigate labor for dimensional inspection of containers at incoming inspection;
• To help prevent bright stock mix-ups by reading the code and confirming the product;
• As an anti-counterfeiting/diversion solution.
Hollander led the initial charge for industry’s use of bar codes to prevent dispensing errors, as well as piloting the use of RFID for Viagra as a potential technology to mitigate counterfeiting. He was also successful lobbying GS1 to formally adopt the Data Matrix code in 2004 at a critical time for pharmaceutical serialization. He is a founding member and served as an initial Tri-Chair of GS1 Healthcare, which serves to develop and implement GS1 standards. Having him advocate for SignaKey feels like a logical extension of his life’s work of making sure pharmaceutical packaging is safe and effective.
About the Author(s)
You May Also Like