Bridge Collapse Triggers Supply Chain Warnings
The tragic collapse of Baltimore’s Francis Scott Key Bridge on Tuesday, March 26, brings attention to America’s business of moving packaged goods.
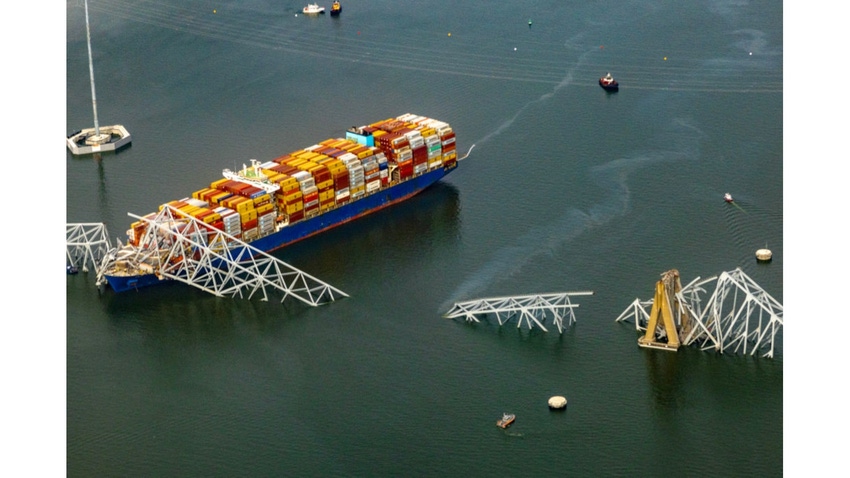
With six dead and one badly injured, it seems inconsiderate to talk about the business implications of the recent shipping accident that caused a 1.6-mile span of bridge to fall into the Patapsco River. My condolences to their families.
But we face serious supply chain challenges because of this collapse that you need to know about.
What happened? Loaded cargo ship MV Dali lost power on its way to the busy Port of Baltimore. With no way to navigate through the channel, the ship hit one of the bridge’s support pilings in the early morning of Tuesday, March 26. Dali personnel issued a mayday before the collision, and thankfully the bridge was shut down to traffic. But eight construction workers were still on the bridge when it fell into the water. Two of them were rescued. The other six are presumed dead.
My colleague Spencer Chin, Senior Editor with Design News, explains why “Bridges and Cargo Ships Don’t Mix.” Bridges are just not able to withstand an impact from a ship that is nearly their same weight, no matter how well they are built and maintained.
Shortcomings of the US supply chain became apparent during the COVID-19 pandemic. But Reuters reports many of the problems with our ports were strengthened and/or fixed, putting the country in a better position to withstand a crisis. “Supply chain experts say U.S. port infrastructure is more resilient than during 2021 and 2022, when they were understaffed and clogged with ships and containers, spiking prices and contributing to inflation as Americans binged on goods purchases during the COVID-19 pandemic.”
This situation isn’t a crisis but will still be disruptive. Immediate challenges of the bridge collapse stem from:
• the indefinite closure of the Port of Baltimore
• rerouting road traffic that would have used the bridge
• higher shipping prices, potentially, in the short term
• tighter shipping availability, potentially, that is likely to slow deliveries
The economic impact will be felt most severely by the Port of Baltimore, but the ripples could be quite far-reaching, according to a report by CBS News.
Many media outlets and supply chain experts are also identifying potential business concerns and offering advice:
USA Today: “How will the Baltimore bridge collapse affect deliveries? What to know after ship collision”
Container xChange, an online marketplace for shipping containers, issued a customer advisory to help companies currently navigating the challenges posed by this event or seeking to comprehend its repercussions on the container shipping industry.
WeFreight shares insightful numbers about the Port of Baltimore in an infographic and explains how shipping companies are responding.
The potential impact on your packaging operations.
Last summer, when a UPS strike appeared imminent, Packaging Digest offered advice on mitigating risk of your logistics operations. Some of that advice is relevant now, too, with updates for the current condition:
• Understand that shipments may take longer and cost more. Do you have the budget? Can your customers wait or will they look for another source?
• Realize the impact of lost product. I’m thinking of the products in shipping containers that are still on the Dali. When, if ever, will they be offloaded? The more expensive a product, the more the loss of a full production run will hurt. Assess the risk of shipping all your products at once through the same channel.
• Work with a third-party logistics company (3PLs) to leverage their extensive network and expertise.
• Assess increasing your made-product inventory vs. running production for just-in-time deliveries to reduce lost sales.
• Realize that your vendors may be affected, too. Assess your raw materials inventory, including replacement parts for packaging machines, vs. just-in-time orders.
This situation is temporary, and we’ll get through it.
About the Author(s)
You May Also Like