The Next Step to Unlocking Plastic Circularity
It’s possible to solve a food-grade recycling challenge using this first-of-a-kind enhanced sorting technology.
March 13, 2024
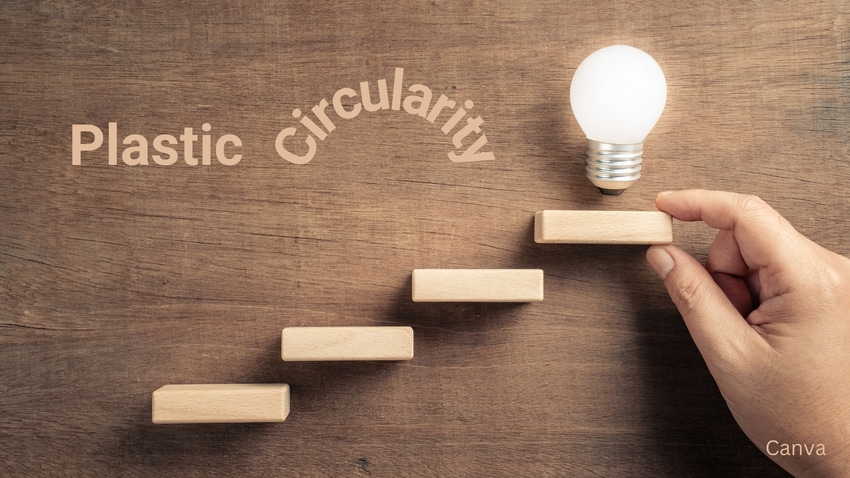
This is an era of increasingly sophisticated technologies. However, from a recycler’s perspective, we are still fumbling in the dark to find an efficient way to produce tailored recycled materials to order.
What if we could deep dive into the waste feedstock and better refine which properties we want to extract from the recycled material? If so, we could use a higher proportion of recycled content to boost the circularity of plastics.
This would require separating packaging by the flow grade of the materials, something that until now was assumed to be too complex.
Differentiating low-viscosity materials from high-viscosity materials would be the next step to enable sorting of post-consumer packaging into mono-polymer food-grade fractions. This is what NextLOOPP is already doing.
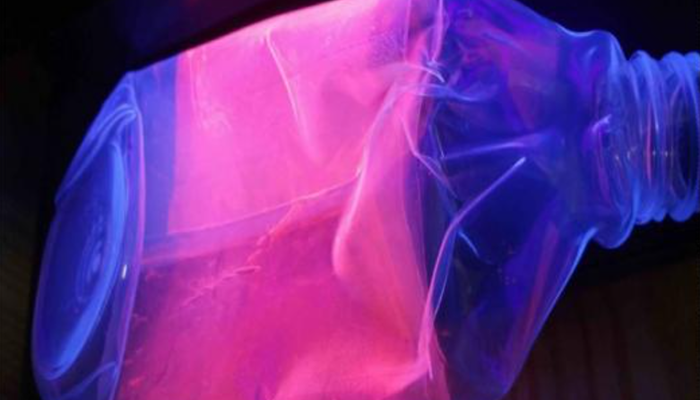
NextLOOP
Since launching in 2020, NextLOOPP has deployed Nextek’s PolyPPrism technology (shown above) to sort post-consumer packaging first into polypropylene and then further into food-grade PP. The 2021 trials at the Tomra Test Centre exceeded the required 95% purity for food grade; the first pass achieved 99.3% purity of sorted packs while the second pass yielded 99.9% purity.
Nextek is now advancing the science-based technology to another level based on the near-infrared (NIR) spectroscopy response of the polymer. As a reminder, the emission of the fluorescent markers illuminated under ultraviolet light identifies the packaging item that can be sorted and ejected.
This allows for a wide range of products to be uniquely separated from a mixed stream of packaging items.
Added markers pinpoint two types of PP packaging.
Nextek can now expand the number of sortable materials using more markers. The team has been trialing a second fluorescent marker on the label so that all food-grade PP packaging is selected on the first pass. In the second pass and based on the second marker, only injection-molded PP is selected. This effectively sorts food-grade injection molded packaging from extrusion-grade PP packaging.
This two-step process was recently trialed at Tomra in Germany. The first pass to separate food-grade PP from nonfood PP resulted in a 100% yield and purity. During the second pass for further sortation, injection-molded PP such as cups and tubs (which have a denser and sturdier structure) were separated from extrusion-molded PP (thinner, more flexible packaging like films and trays) with 97% separation success.
This can dramatically reduce the current challenges and complexities of recycling.
By enhancing the sorting process NextLOOPP is a step closer to closing the loop on specific packaging types to reach higher rates of quality recycled content. And that’s another step toward true plastic circularity.
About the Author(s)
You May Also Like