Packaging Design
SnapSlide Rx closure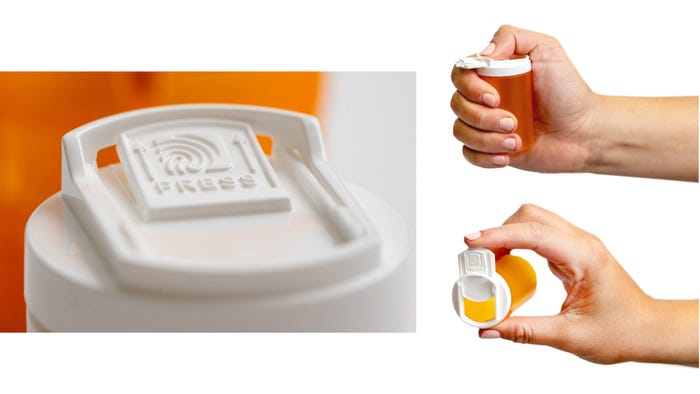
Pharmaceutical Packaging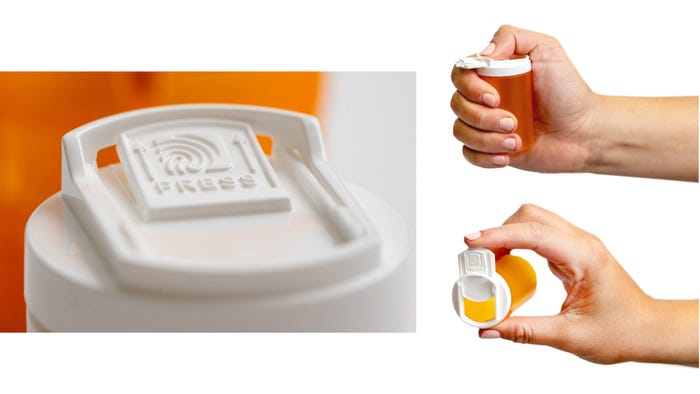
Torque-Free Rx Closure Allows for Single-Handed OperationTorque-Free Rx Closure Allows for Single-Handed Operation
The child-resistant cap for amber vials features a two-step opening procedure for people with limited dexterity.
Sign up for the Packaging Digest News & Insights newsletter.