Labeling
Sojo Shield traceability uses AI, QR codes, blockchain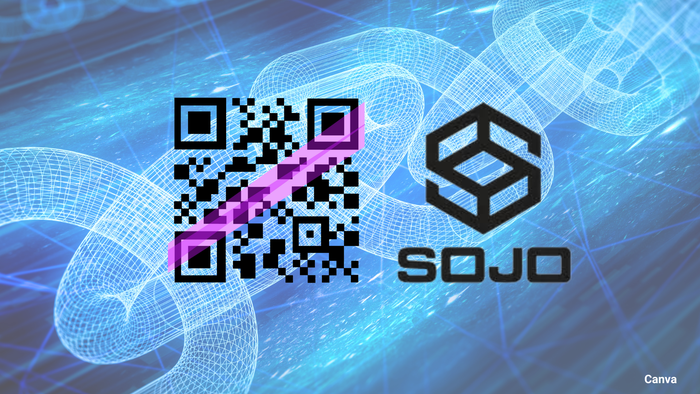
Food Safety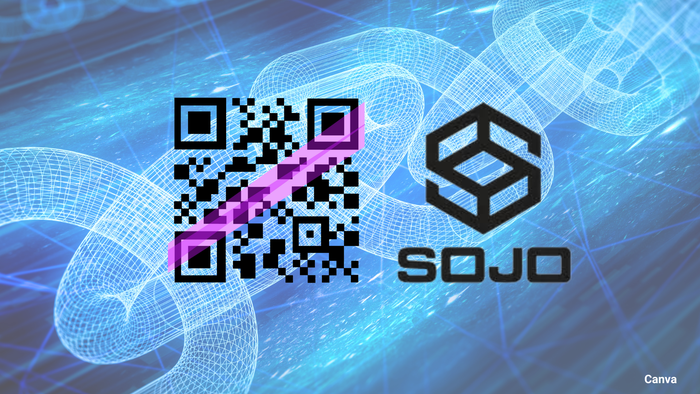
Where’s Your Packaged Food? FDA Will Need to KnowWhere’s Your Packaged Food? FDA Will Need to Know
Feeling pressure from FDA's traceability deadline? Sojo Shield is a game-changing, real-time solution that uses blockchain, geolocation, AI, and QR codes.
Sign up for the Packaging Digest News & Insights newsletter.