Benefits of new full-color, single-face, laminate packaging
January 30, 2014
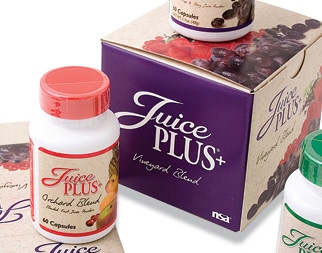
pdx1004juiceplus1
National Safety Assoc. (NSA) Corp., Collierville, TN, says its Juice Plus+ product line has enjoyed double-digit market growth for the last 15 years. This didn't stop the brand owner from looking at how a packaging update could 1.) excite its direct sales franchisees2.) reinforce the product's benefits by visually depicting the nutritious produce used to create the powdered juice concentrate (PJC)
3.) better address the product consumer base
4.) optimize the packaging structure's functionality to enable easy reclosure for the product's two-stage pack-out process.
Woman-dominated sales force
“Almost 40 years ago, we actually pioneered the home and office fire prevention system” says John Blair, vp of product and research for NSA Corp. “Our previous products were more of the appliance type—they were the fire prevention system, water filtration at point of use in the home, and air filtration in the home and office.
“We entered the nutrition business some years ago,” Blair adds. “Since that time, we have gravitated from a sales force that was made up of mostly men to one that's mostly women. So we wanted the packaging to be softer [to reflect the move from an appliance-based business to nutritionals business] and more appealing to female consumers and distributors.”
pdx1004juicebty2
Working with its design agency Bray Leino Ltd, NSA designed new corrugated shippers. Light tan backgrounds with printed textures soften the overall look. The fruits and vegetables used to create each product are visually highlighted with vibrant photography. Previously, the packaging used abstract graphics to represent the produce.Design that goes beyond just graphics
More than the graphics were updated in this project. NSA also worked with design-and-supply company Peek Packaging to create a structure that would better fit the Juice Plus+ pack-out process.
“In our discussions with NSA, we found that when they receive the filled shippers that they actually open the box back up, place literature inside the shipper, and reclose the box,” Bob Peek, owner of Peek Packaging, recalls. “The problem NSA was having is with the tie-locks. Tie locks use little slits to make sure a tab once tucked in doesn't come undone easily. When a corrugated box with tie locks is reopened, the box tends to tear, which disfigures the top.”
Peek Packaging designed a new packaging structure that used a friction lock on the tuck instead.
“We added two little bumps to the sides of the top box panel. This design helps keep the box from accidentally being opened, but still allows the box to be opened and closed repeatedly without damage,” remarks Peek.
To quicken the pack-out process for NSA's copacker Natural Alternatives Intl Inc. (NAII), Peek Packaging also changed the base of the corrugated shipper to an auto-bottom. This simplifies box erection as a line worker would only need to press on the edges of the box to move the box's tuck tabs into place, thus creating a secure base.
Peek was so confident of his company's solution that he had a short run of the boxes manufactured before he even had the client sign-off.
pdx1004juiceplus5
“I didn't have a contract; I wasn't doing their boxes,” Peek recalls. “But I went ahead and contracted with my box supplier to have a short run of 1,000 boxes manufactured on my dime. NSA had a show coming up. I knew that they would want to show off these new boxes. I invested the money on solving the problem because I also knew that because the boxes are single-face, laminate that the lead time was long.”Tuned colors
Before the files could be reproduced on press, Peek Packaging's supplier Allpak Trojan fine-tuned the color and layouts.
“Our prepress equipment, all our computers, everything, are specific to the process of preparing art files for our printing presses,” explains Jackie D'Ambrosio, an account representative for Allpak Trojan. “Our technicians use the equipment to show customers exactly what will yield on our printing presses. So while a proofing printer in a graphic artist's studio might have been calibrated a certain way and produced a proof that reflects those adjustments, the reality is that the file might look very different on a printing press than it did on the proof.”
The combination of brightly colored photography and the four-color beige background made file preparation and color correction challenging.
“The four-color process background was extremely sensitive to the slightest shift in any of the processing,” D'Ambrosio recalls. “You've got this vignette with fruits and vegetables that are very saturated, and all these graphic elements are all tied together on the same four process plates. If you manipulate, say the carrot, you can cause a very strange coloration shift in the background that you didn't intend.”
To ensure that Allpak Trojan met customer expectations, it used a Rampage workflow that enabled it to rasterize the file only once before output to any of the package printer's presses or devices.
“We RIP (raster image process) the file once for consistency of data,” says D'Ambrosio. “This way you don't risk any corruption of the file or changes to the file [not being present in all versions].”
Proofs were made using an Epson inkjet printer, which is profiled to match the package printer's presses.
Once the final proof was approved, the package printer and converter used a Screen PlateRite Ultima CtP device to image the aluminum plates. To help reduce color shifts, stochastic screening was used to image the dots.
Box manufacturing
pdx1004juicebty1
Imaged plates are mounted onto a KBA Rapida, eight color plus coating press, which prints the solid bleached sulfate (SBS) sheets that become the outmost layer of the shipper.The printed SBS sheets are laminated to the open-face corrugated web using a laminator from Asitrade, a tradename belonging to equipment supplier Bobst Group. Rolls of liner board and medium are loaded onto the Asitrade, which then flutes the medium and applies it to the liner. The open-face corrugated web is topped with the printed SBS top sheets. The Asitrade then cuts the finished corrugated web back down to sheets, which are stacked in the machine's delivery.
The composed single-face sheets are moved to the Allpak Trojan's finishing area, where postpress operators use a Bobst CER with a laser-cut die to die-cut the composed single-face sheets.
“What makes our boxes superior is that we cut flatbed with a counter die and matrixes and we cut from the backside of the box,” D'Ambrosio comments. “A lot of people who do this style of box—the single-face, litho-lam—cut from the topside of the box. This causes score lines to fracture when the box is folded.”
The die-cut carton blanks are then run through a Bobst Domino straight-line gluer, which converts the blanks into auto-bottom boxes.
The boxes are carefully case-packed to prevent warping or bending while in transit 1,200 miles to the copacker.
Product manufacturing, packing
Juice Plus+ products for U.S. distribution are manufactured at NAII's facility in San Marcos, CA.
The JPC is manufactured according to NSA specifications, then packed into capsules supplied by Capsugel, a division of Pfizer Inc.
Filled capsules are loaded onto the packing line using a hopper hoist; HDPE bottles enter the packing line from a Kaps-All unscrambler.
One of NAII's many slat fillers, which include models from Integrated Packaging Systems Inc. and IMA Swiftpack, are used to dispense the capsules. Filled bottles are first checked for weight by an Alpha checkweigher from All-Fill Inc.; either a Lock Inspections Systems Inc. or a Loma Systems metal detector ensures that bottles have nometal containments.
To further ensure consumer safety, an Auto-Mate induction sealer secures liners over bottles' openings. An Arol rotary capper closes containers. Shrink equipment from either Marburg Industries or PDC Intl Corp. is used to apply tamper-evident bands around the Juice Plus+ flip-top caps.
NAII flexo-prints the labels using an Arpeco Ink press (Early this year, the Arpeco brand was acquired by Mark Andy and has been folded into its Rotoflex line) using DuPont Cyrel plates. Label artwork is prepped using software from EskoArtwork.
A Bronco labeler from NJM/CLI Packaging Systems Intl places the printed labels onto the bottles. Lot codes and expiration dates are placed by either a Videojet printer on the bottom of the HDPE container or by a Markem thermal-transfer printer onto the label.
Positive feedback
The new shippers have been well received. NSA partially attributes the continued market growth of Juice Plus+ in Europe and the strength of U.S. product demand to its packaging update.
More information is available: |
Peek Packaging, 760/438-1616. www.peekpackaging.com |
Natural Alternatives International Inc., 800/848-2646. www.nai-online.com |
AllpakTrojan, 425/227-0400. www.allpaktrojan.com |
All-Fill Inc., 800/334-1529. www.alphacheckweighers.com |
Arol USA Inc., 678/318-1290. www.arol.com |
Auto-Mate Technologies Inc., 631/369-3903. www.automatetech.com |
Bobst Group North America Inc., 704/587-2450. www.bobst.ch |
Bray Leino Ltd., +44 1598 760 700. www.brayleino.co.uk |
Capsugel, a division of Pfizer Inc., 908/901-8000. www.capsugel.com |
Epson America Inc., 800/463-7766. www.proimaging.epson.com |
IMA Swiftpack, +44 789 400 880. www.swiftpack.com |
Integrated Packaging Systems Inc., 973/664-0020. www.ipsnj.com |
KAPS-ALL Packaging Systems Inc., 631/727-0300. www.kapsall.com |
KBA North America Inc., part of the Koenig & Bauer AG group, 800/522-7521. www.kba.com |
Lock Inspection Systems Inc., 800/227-5539. www.lockinspection.com |
Loma Systems, an ITW Co., 800/872-5662. www.loma.com |
Mark Andy Inc., 636/532-4433. www.markandy.com |
Marburg Industries, 760/727-3762. www.marburgind.com |
Markem Corp., 800/322-0057. www.markem.com |
NJM/CLI Packaging Systems Intl, 800/432-2990. www.njmcli.com |
PDC Intl Corp., 203/853-1516. www.pdc-corp.com |
Rampage Systems Inc., 781/891-9400. www.rampageinc.com |
Screen (USA), 800/372-7737. www.screenusa.com |
Videojet Technologies Inc., 800/843-3610. www.videojet.com |
About the Author(s)
You May Also Like